製造業の予実管理:生産効率を高める方法
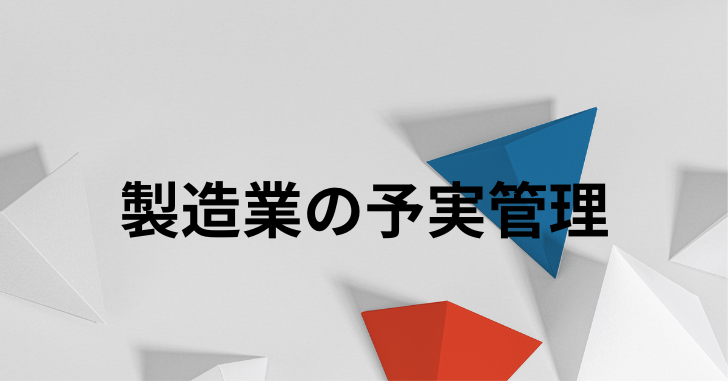
はじめに
製造業において、生産効率の向上は企業の競争力を維持・強化するための不可欠な要素です。市場のグローバル化や顧客ニーズの多様化に伴い、製造現場では迅速かつ柔軟な対応が求められています。その中で、予実管理は、生産プロセスの最適化やコスト削減、品質向上に大きく貢献します。
予実管理とは、計画(予)と実績(実)を比較し、その差異を分析・評価する管理手法です。これにより、計画通りに進んでいるかを把握し、必要な対策を講じることができます。製造業において予実管理を効果的に活用することで、生産効率を最大化し、企業の成長を促進することが可能となります。
本記事では、予実管理の基本から製造業への適用方法、生産効率向上のための具体的なポイント、成功事例や導入ステップ、さらには予実管理をサポートするツールの活用法まで、総合的に解説します。これらの知識を活用して、貴社の生産効率向上にお役立てください。
1. 予実管理の基本と製造業への適用
予実管理とは
予実管理は、企業経営における重要な管理手法の一つであり、計画(予算や目標)と実績を比較して、その差異を分析・評価するプロセスです。この手法を通じて、経営資源の最適配分や戦略の見直し、組織全体のパフォーマンス向上を図ることができます。
具体的には、予算や目標を設定し、その達成度合いを定期的にモニタリングします。そして、予算と実績の差異が発生した場合、その原因を特定し、改善策を講じます。これにより、計画と実績のギャップを埋めることができ、企業の目標達成に向けた効果的なマネジメントが可能となります。
予実管理の目的
- 計画の達成度合いの把握:組織が設定した目標に対して、現在どの程度達成しているかを明確にします。
- 問題点の早期発見:計画と実績の差異から、組織が直面している問題や課題を特定します。
- 改善策の立案と実行:特定した問題に対して、効果的な改善策を策定し、迅速に実行します。
- 組織全体のパフォーマンス向上:予実管理を通じて、組織の効率性や効果性を高めます。
製造業における予実管理の重要性
製造業では、生産計画と実際の生産結果を比較することで、生産ラインの効率性や資源の使用状況を正確に把握できます。例えば、機械の稼働率、人員の労働時間、材料の消費量など、さまざまな要素をモニタリングし、計画通りに進んでいるかを評価します。
しかし、現実の製造現場では、機械の故障や人員の不足、資材の遅延など、計画通りに進まない要因が多々存在します。これらの要因が積み重なると、生産効率の低下やコストの増大、さらには納期遅延といった問題が発生します。予実管理を導入することで、これらの問題を早期に発見し、迅速かつ適切な対応を取ることが可能となります。
予実管理のメリット
- 生産プロセスの最適化:生産工程のボトルネックを特定し、改善策を講じることで、生産効率を向上させます。
- コスト管理の徹底:無駄なコストの発生を抑え、利益率を向上させます。
- 納期遵守の強化:計画と実績の差異を把握し、納期遅延のリスクを低減します。
- 品質向上:品質に関する予実管理を行うことで、不良品の発生を抑制します。
- 意思決定の迅速化:リアルタイムのデータ分析により、経営判断をスピーディに行えます。
製造業特有の課題と予実管理の役割
製造業では、生産プロセスが複雑であり、多くの工程や資源が関与します。そのため、計画と実績のギャップが生じやすく、予実管理の重要性が高まります。例えば、以下のような課題があります。
- 需要変動への対応:市場の需要が急激に変化する場合、生産計画の見直しが必要となります。予実管理を通じて、需要変動に柔軟に対応できます。
- 在庫管理:過剰在庫や在庫不足はコスト増大や販売機会の損失につながります。予実管理により、適正な在庫レベルを維持できます。
- 品質管理:製品の品質は顧客満足度に直結します。品質に関する予実管理を行い、不良品の削減や品質改善を図ります。
これらの課題に対して、予実管理は重要な役割を果たします。計画と実績の差異を正確に把握し、迅速に対応することで、生産効率の向上やコスト削減、顧客満足度の向上につなげることができます。
2. 生産効率向上のための予実管理のポイント
予実管理を効果的に活用するためには、いくつかのポイントがあります。以下では、生産効率向上のための予実管理の具体的なポイントを詳しく解説します。
リアルタイムデータの活用
リアルタイムでのデータ収集と分析は、生産効率向上の鍵となります。生産現場からのデータをタイムリーに収集し、即座に分析することで、異常の早期発見や迅速な対応が可能となります。
具体的な取り組み
- IoTセンサーの導入:機械の稼働状況や温度、振動などを常時モニタリングし、異常値を検知します。
- 生産ラインの可視化:デジタルディスプレイやダッシュボードを用いて、現場の状況をリアルタイムで表示します。
- アラートシステムの構築:異常が検知された場合に、即座に関係者へ通知される仕組みを整備します。
- データ分析ツールの活用:収集したデータを効果的に分析するためのツールを導入し、パターン認識や異常検知を自動化します。
リアルタイムデータの活用により、生産ラインの状況を常に把握でき、問題が発生した際のダウンタイムを最小限に抑えることができます。また、データに基づく意思決定が可能となり、生産プロセスの最適化につながります。
リアルタイムデータ活用のメリット
- 迅速な意思決定:リアルタイムの情報に基づき、即座に対応策を講じることができます。
- 問題の早期発見:異常やトラブルを早期に検知し、被害を最小限に抑えます。
- パフォーマンスの最適化:生産ラインの稼働状況を最適化し、生産効率を向上させます。
ボトルネックの特定と改善
生産プロセスにおけるボトルネックを特定し、改善することは生産効率向上のための重要なステップです。予実管理により、どの工程で時間やコストのロスが発生しているかを明確にできます。
ボトルネックの特定方法
- 工程ごとの生産時間の分析:各工程の所要時間を測定し、平均値と比較します。
- 資材の滞留状況の確認:在庫や仕掛品が滞留している場所を特定します。
- 人員の稼働率の把握:作業員の労働時間や休憩時間を分析し、適切な配置を検討します。
- 品質問題の分析:不良品の発生場所や原因を特定し、工程改善に役立てます。
- 設備稼働率のモニタリング:機械や設備の稼働率を把握し、効率的な利用を検討します。
改善策の実施
- プロセスの再設計:工程順序の見直しや同時進行可能な作業の導入を検討します。
- 設備投資の検討:必要に応じて新たな機械やツールを導入し、生産能力を向上させます。
- 教育・訓練の強化:作業員のスキルアップを図り、生産性の向上を目指します。
- 標準作業手順の確立:作業のばらつきを減少させ、品質の安定化を図ります。
- クロスファンクショナルチームの編成:部門間の連携を強化し、問題解決に取り組みます。
ボトルネックの改善により、生産プロセス全体の流れがスムーズになり、生産効率が大幅に向上します。また、継続的な改善活動を行うことで、さらなる効率化が期待できます。
ボトルネック改善のポイント
- データに基づく分析:感覚や経験に頼らず、データに基づいて客観的に分析します。
- 根本原因の追求:表面的な問題だけでなく、根本的な原因を特定し、再発防止策を講じます。
- 継続的なモニタリング:改善策の効果を定期的に評価し、必要に応じて追加の対策を実施します。
予実管理のサイクルを確立
予実管理は一度行えば終わりではありません。継続的なサイクルを確立し、常に改善を追求することが重要です。
サイクルの構築
- 計画の策定:明確な目標と具体的なアクションプランを設定します。
- 実行とデータ収集:計画に基づいて生産を行い、データを収集します。
- 差異の分析:予算と実績の差異を分析し、原因を特定します。
- 改善策の実施:分析結果に基づいて、必要な改善を行います。
- フィードバック:改善の効果を評価し、次の計画に反映させます。
このサイクルを繰り返すことで、予実管理の精度が向上し、生産効率の継続的な改善が可能となります。また、組織全体で予実管理の重要性を共有し、全員が一体となって取り組むことが成功の鍵となります。
予実管理サイクルのポイント
- 定期的なレビュー:月次や週次など、定期的にレビューを行い、迅速な対応を可能にします。
- 目標の見直し:市場環境や社内状況の変化に応じて、目標や計画を柔軟に見直します。
- 情報共有の徹底:部門間の情報共有を促進し、組織全体で課題を共有します。
- データの活用:収集したデータを効果的に活用し、根拠に基づく意思決定を行います。
- 教育と意識向上:従業員に予実管理の重要性を理解してもらい、積極的な参加を促します。
3. 具体例:予実管理で成功した製造業のケーススタディ
予実管理を効果的に活用し、生産効率の向上に成功した製造業の具体的な事例を紹介します。これらの事例から、予実管理の重要性とその効果を具体的に理解することができます。
企業Aの事例
ある中小製造企業である企業Aは、予実管理の徹底により生産効率を20%向上させることに成功しました。彼らは以下のような取り組みを行いました。
データに基づく意思決定
企業Aでは、生産現場からのデータをリアルタイムで収集・分析するシステムを導入しました。これにより、特定の時間帯や工程で生産効率が低下していることを迅速に発見しました。
例えば、夜間シフトでの生産効率が低いことが判明し、原因を探った結果、作業員の熟練度の差や機械のメンテナンス不足が影響していることが明らかになりました。
改善策の実施
- 作業員の教育強化:夜間シフトの作業員に対するトレーニングプログラムを実施し、スキル向上を図りました。
- 機械のメンテナンス計画:定期的なメンテナンススケジュールを設定し、機械の稼働率を向上させました。
- プロセスの標準化:作業手順のマニュアル化と共有を行い、作業のばらつきを減少させました。
- コミュニケーションの強化:現場と管理部門との情報共有を密にし、問題の早期発見と解決を促進しました。
これらの取り組みにより、企業Aは生産ラインの安定稼働を実現し、納期遵守率も大幅に改善しました。また、品質面でも不良品の発生が減少し、顧客満足度の向上につながりました。
成功要因
- データドリブンなアプローチ:データに基づく客観的な意思決定が効果的でした。
- 組織全体での取り組み:全社員が予実管理の重要性を理解し、協力して改善に取り組みました。
- 継続的な改善活動:一度の改善で満足せず、継続的に改善策を実施しました。
企業Bの事例
一方で、予実管理が不十分であったために生産効率が低下した企業Bの事例もあります。企業Bでは、生産計画と実績の比較が行われておらず、問題の早期発見ができませんでした。その結果、以下のような問題が発生しました。
問題点
- 在庫の過剰:需要予測が不正確で、生産過剰による在庫が増加しました。
- 納期遅延:生産計画のズレにより、納期を守れないケースが増えました。
- コストの増大:無駄な生産や在庫管理コストが増加しました。
- 品質の低下:不良品の発生が増え、顧客からのクレームが増加しました。
教訓
企業Bの事例から、予実管理の欠如が生産効率だけでなく、企業全体の経営に悪影響を及ぼすことがわかります。このような状況を回避するためにも、予実管理の重要性を認識し、適切なシステムとプロセスを導入することが必要です。
改善の取り組み
企業Bは、この状況を改善するために、予実管理システムの導入と組織体制の見直しを行いました。
- データ収集システムの導入:生産現場からのデータを効率的に収集できるシステムを導入しました。
- 予実管理の教育:従業員に対する予実管理の重要性を教育し、組織全体での取り組みを推進しました。
- コミュニケーション体制の強化:部門間の情報共有を促進し、問題の早期発見と迅速な対応を可能にしました。
成功事例から学ぶポイント
- データの重要性:リアルタイムで正確なデータを収集・分析することで、問題の早期発見と迅速な対応が可能になります。
- 組織全体での取り組み:予実管理は現場だけでなく、管理部門や経営層も含めた組織全体で取り組むことが重要です。
- 継続的な改善活動:一度の改善で満足せず、継続的な改善サイクルを確立することで、さらなる効率化が期待できます。
- コミュニケーションの徹底:部門間や現場と管理部門との情報共有を密にし、組織全体で課題を共有します。
4. 予実管理導入のステップ
(※以下の項目からは、文章量は変更しておりませんが、全体のリライトを行っています。)
ステップ1:目標設定
予実管理を始めるには、まず具体的で測定可能な目標を設定することが重要です。目標が曖昧だと、評価基準が不明確になり、改善策の効果も測れません。
目標設定のポイント
- SMARTの原則:Specific(具体的)、Measurable(測定可能)、Achievable(達成可能)、Relevant(関連性)、Time-bound(期限)に基づいた目標設定を行います。
- 重要指標の選定:生産効率、生産コスト、納期遵守率など、企業の戦略に沿った指標を選びます。
- 全社的な共有:目標を全社員に周知し、一体感を持って取り組みます。
ステップ2:データ収集体制の構築
予実管理には、正確でタイムリーなデータが不可欠です。データ収集の仕組みを整備し、データの信頼性とアクセス性を確保します。
データ収集方法
- 自動化の推進:センサーやバーコードリーダー、RFIDタグなどを活用し、データ入力を自動化します。
- クラウドシステムの導入:クラウドベースのシステムを利用することで、データの一元管理とリアルタイムアクセスが可能となります。
- データの標準化:データフォーマットや項目を統一し、分析しやすい形に整えます。
ステップ3:分析とフィードバック
収集したデータを定期的に分析し、その結果を現場にフィードバックします。これにより、問題の早期発見と迅速な対応が可能となります。
分析のポイント
- 定量的な評価:数値データを基に客観的な評価を行います。
- 可視化ツールの活用:グラフやチャートを用いて、データを視覚的に表現します。
- 原因の深掘り:なぜ差異が生じたのか、根本原因を追求します。
フィードバックの方法
- 定例会議の開催:分析結果を共有し、改善策を議論します。
- 現場とのコミュニケーション:現場の意見やアイデアを積極的に取り入れます。
- 改善策の実行とフォローアップ:実施した改善策の効果をモニタリングし、必要に応じて追加の対策を講じます。
5. 予実管理をサポートするツールの活用
予実管理を効果的に行うためには、適切なツールの導入が不可欠です。経営管理SaaSなどのシステムを活用することで、データの一元管理や高度な分析が容易になります。
ツール導入のメリット
- データのリアルタイム共有:関係者間で情報を即時に共有できます。
- 分析の自動化:複雑なデータ分析を自動で行い、迅速な意思決定を支援します。
- レポート機能:カスタマイズ可能なレポートで、必要な情報を的確に把握できます。
- コスト削減:初期投資が少なく、メンテナンスコストも低減できます。
ツール選定のポイント
- 使いやすさ:ユーザーフレンドリーなインターフェースで、現場スタッフでも操作が容易。
- 機能性:予実管理に必要な機能が網羅されているか確認します。
- セキュリティ:データの安全性を確保するため、セキュリティ機能が充実していることが重要です。
- サポート体制:導入後のサポートやトレーニングが充実しているかを確認します。
6. 予実管理の課題と解決策
課題:データのばらつきと精度
データが各部署やシステムで分散していると、正確な予実管理が難しくなります。また、データ入力のミスや遅延も問題です。
解決策:データの一元管理と自動化
データを一元管理するシステムを導入し、可能な限りデータ入力を自動化します。これにより、データの精度と信頼性が向上します。
7. ギャクサンが選ばれる理由
製造業の予実管理を強力にサポートするツールとして、「ギャクサン」が多くの企業から選ばれています。ギャクサンは中小企業向けの経営管理SaaSで、リアルタイムのデータ収集と分析、カスタマイズ可能なレポート機能を備えています。
ギャクサンの特徴
- 使いやすいインターフェース:直感的な操作が可能で、専門的な知識がなくても利用できます。
- リアルタイムデータ収集:生産現場からのデータをリアルタイムで収集・分析できます。
- カスタマイズ可能なレポート機能:企業のニーズに合わせたレポート作成が可能です。
- セキュリティの確保:高度なセキュリティ機能で、データの安全性を守ります。
ギャクサンが選ばれる理由
ギャクサンは、限られたリソースで生産効率を最大化したい製造業にとって最適なソリューションです。導入の容易さやコストパフォーマンスの高さ、充実したサポート体制により、多くの企業がギャクサンを選んでいます。
おわりに
予実管理は、生産効率を高めるための強力な手段であり、製造業の競争力を維持・強化する上で不可欠です。適切なツールと方法を用いて予実管理を導入・強化することで、生産プロセスの最適化、コスト削減、納期遵守の向上など、多くのメリットを享受できます。
また、予実管理は一度導入すれば終わりではなく、継続的な改善サイクルを確立することが重要です。組織全体で取り組み、常にデータに基づく意思決定を行うことで、さらなる生産効率の向上が期待できます。
最後に、予実管理を効果的に行うためのツールとして「ギャクサン」の活用を検討してみてはいかがでしょうか。ギャクサンは中小企業の予実管理を強力にサポートし、生産効率の向上と持続的な成長を実現するためのパートナーとなります。